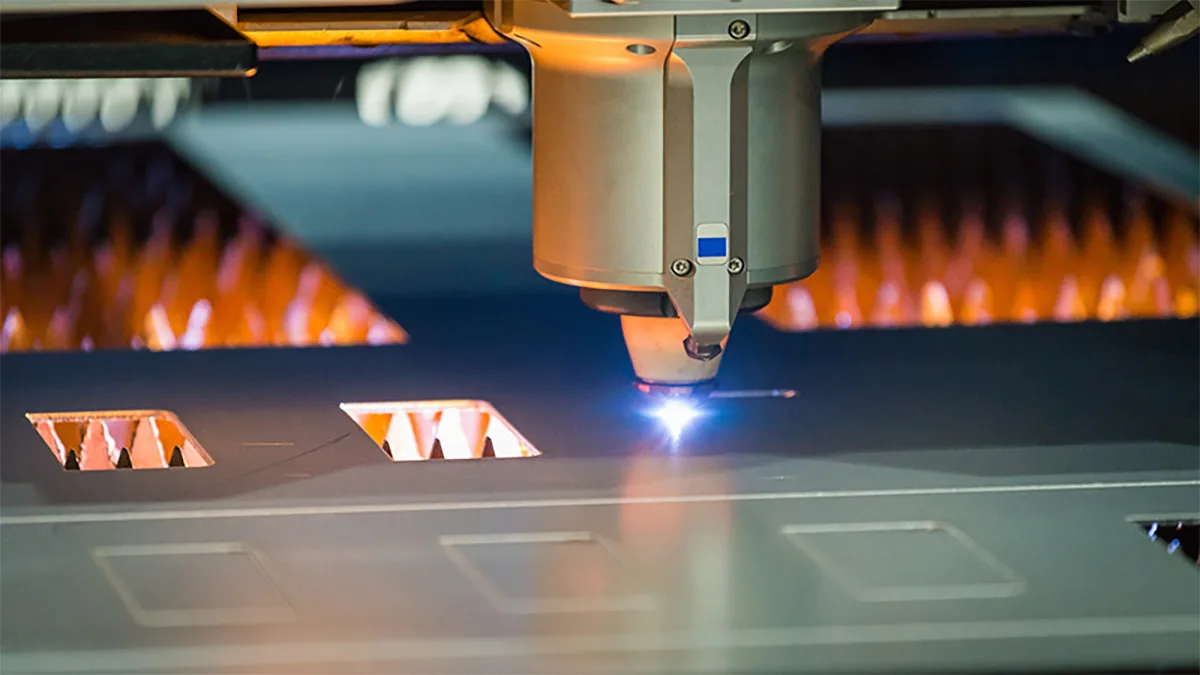
When Metals Face Infernal Trials
Beside molten lava flows from volcanic eruptions, within the corrosive salt spray of deep-sea drilling platforms, and under the thousand-degree heat of spacecraft re-entering the atmosphere, one metal retains its elegant silvery-white luster—stainless steel. While ordinary steel rusts in humid air and aluminum alloys soften under high temperatures, stainless steel demonstrates astonishing adaptability. During the 2011 Fukushima nuclear disaster in Japan, the only metal components unaffected by seawater corrosion were stainless steel products. In 2023, during SpaceX’s Starship test flight, the 304 stainless steel used in its fuel tanks withstood extreme temperature fluctuations from -183°C to 800°C in liquid oxygen-methane fuel. What material science secrets lie behind these real-world cases?
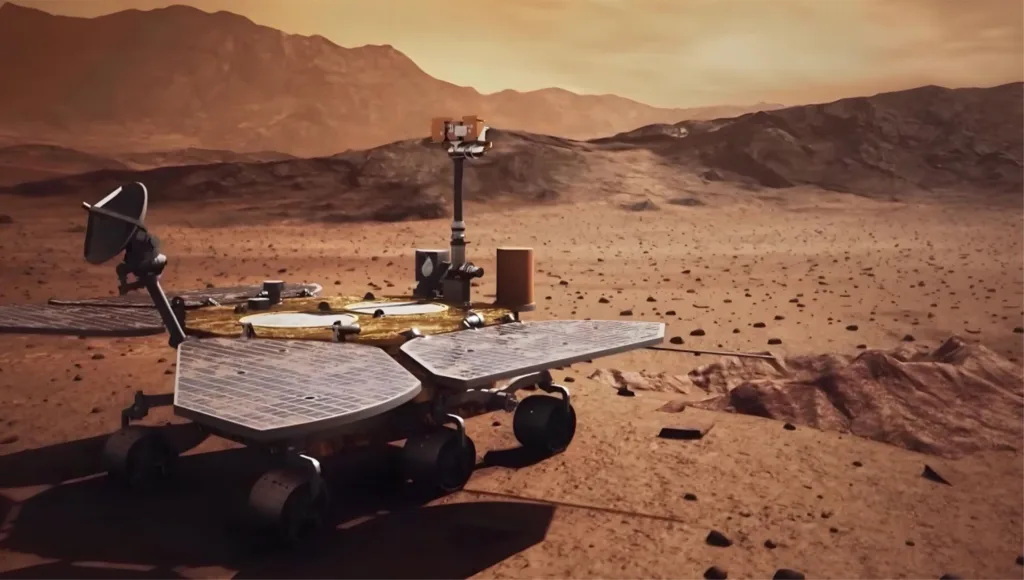
Life-and-Death Barrier: The Miracle of Chromium’s Oxide Film
The Metal’s “Self-Sacrificial Defense”
In 1913, British metallurgist Harry Brearley accidentally discovered an alloy steel containing 12% chromium that remained unscathed in acid rain while searching for gun barrel materials. This serendipitous finding revealed stainless steel’s core secret: a nanoscale oxide film constructed by chromium atoms on the metal surface.
When chromium content exceeds 10.5%, each chromium atom bonds with oxygen to form a dense Cr₂O₃ oxide film, only 3–5 nanometers thick. This transparent protective layer self-repairs at 0.1 μm/s, employing a “counterattack-as-defense” mechanism: when the surface is damaged, chromium atoms immediately recombine with oxygen, akin to rapid scabbing on a skin wound.
Property | Chromium Oxide Film | Iron Oxide Film |
Density (%) | 97 | 65 |
Thermal Expansion (×10⁻⁶/°C) | 7.2 | 12.5 |
Resistivity (Ω·cm) | 10¹² | 10⁶ |
Hardness (HV) | 1800 | 500 |
Molecular-Level Fortifications
Transmission electron microscopy reveals that the Cr₂O₃ film exhibits a honeycomb-like crystalline structure. Its lattice constant (0.514 nm) mismatches with the iron matrix (0.286 nm), enhancing adhesion through structural disparity. Remarkably, the film’s volume is 30% larger than the metal matrix, generating compressive stress during thermal expansion to tighten the protective layer.
At 800°C, ordinary carbon steel oxidizes at 2 mm/h, while 304 stainless steel oxidizes at only 0.02 mm/year. NASA experiments show that 316L stainless steel (18% Cr) in simulated Martian atmosphere (95% CO₂) experiences a mere 0.3 mg/cm² weight loss over 1,000 hours.
Trial by Fire: Decoding Survival Laws Under High Temperatures
Dual Defense: Thermodynamics & Kinetics
Above 570°C, FeO oxide layers on ordinary steel crack due to volumetric expansion. In contrast, stainless steel’s Cr₂O₃ film boasts a higher melting point (2,435°C) and lower thermal expansion coefficient (7.3×10⁻⁶/°C), remaining stable at 1,200°C. A 2018 study by Germany’s Max Planck Institute found that adding 2% yttrium quintuples the oxide film’s lifespan at 1,400°C.
The Art of Phase Transformation Control
Austenitic stainless steel (e.g., 304) stabilizes its face-centered cubic structure via nickel, retaining over 50% elongation even when red-hot. Ferritic stainless steel, strengthened by molybdenum solid solutions, maintains a yield strength of 120 MPa at 900°C. In 2019, Shanghai Jiao Tong University developed FeCrAl stainless steel, achieving a creep life exceeding 100,000 hours under simulated nuclear reactor conditions (650°C/15 MPa).
Key Principles
– Entropy Increase: Cr₂O₃ maintains negative ΔG until 1,200°C.
– Lattice Matching: Oxide film-metal matrix lattice mismatch <5%.
– Dynamic Equilibrium: Cr³+ diffusion rate balances oxidation rate.
Applications
– Jet engine combustors (800–1,000°C): Nickel alloys with 20% Cr.
– Nuclear reactor cladding (600°C/high-pressure steam): 316L stainless steel with >40-year service life.
– Automotive turbochargers (950°C): Ferritic stainless steel withstands >10⁵ thermal fatigue cycles.
Doping with rare earth elements (Y, La) raises oxide film spallation temperature from 900°C to 1,300°C. Recent research by the Institute of Metal Research, Chinese Academy of Sciences, shows that adding 0.1% yttrium triples oxide film adhesion energy.
Corrosion Warfare: Cracking the Code Against Chemical Attacks
Terminator of Electrochemical Corrosion
In seawater, ordinary carbon steel dissolves as an anode at 0.1 mm/year. Stainless steel’s passive film elevates its electrode potential from -0.44 V to +0.2 V—a 0.64 V leap equivalent to insulating the metal. A 2022 Norwegian University study found super duplex stainless steel corrodes at just 0.001 mm/year in North Sea oilfields.
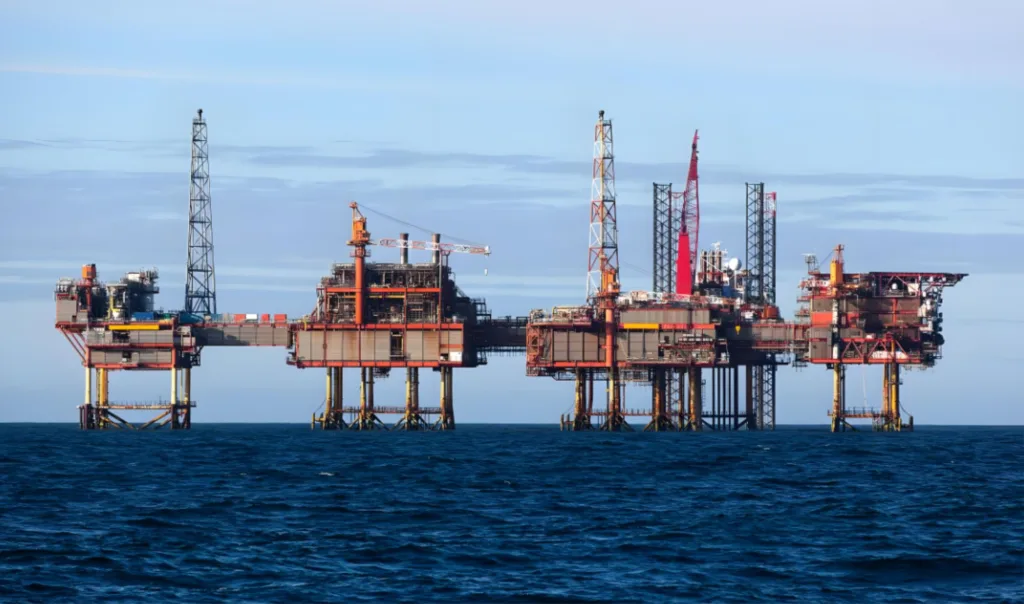
Special Forces: Synergy of Alloying Elements
– Molybdenum: Forms MoO₄²⁻ in Cl⁻ environments to seal oxide film defects.
– Nitrogen: Enhances pitting resistance equivalent (PREN = Cr% + 3.3Mo% + 16N%).
– Copper: Induces protective Cu₂O layers in acidic environments.
Stainless steel pioneers active defense, contrasting traditional passive methods (coatings, cathodic protection). Its passivation mechanisms include:
– Anodic polarization curve shifts right (passive current density <0.1 μA/cm²).
– Breakdown potential rises to +1.0 V (vs SCE).
– Surface zeta potential shifts from -20 mV to +50 mV.
Extreme Challenges
– Aqua Regia (3:1 HCl:HNO₃): Mo-enhanced super stainless steel lasts 1,000 hours.
– North Sea Oilfields: Duplex stainless steel resists 20,000 ppm Cl⁻ + 8 MPa pressure.
– Pharmaceutical Equipment: 316L stainless steel corrodes <0.01 mm/year in pH=1 organic acid.
Atomic probe tomography (APT) reveals:
– Cr/Fe ratio plummets from 18% to 5% at pitting initiation.
– Mo forms protective MoO₂²⁻ layers at pit fronts.
– Nitrogen triples repassivation rate.
Baosteel’s BFS-1 stainless steel corrodes at 0.02 mm/year in 98% sulfuric acid—20 times better than traditional 316L.
Extreme Environment Applications
Deep-Sea Guardian: Mariana Trench Protector
China’s Striver manned submersible employs Ti-6Al-4V/316L composite structures. At 10,909 meters depth, stainless steel components withstand 110 MPa pressure while resisting pH 2.8 hydrothermal corrosion. Seals made of Nitronic 60 stainless steel (0.4% N) fend off hydrogen sulfide.
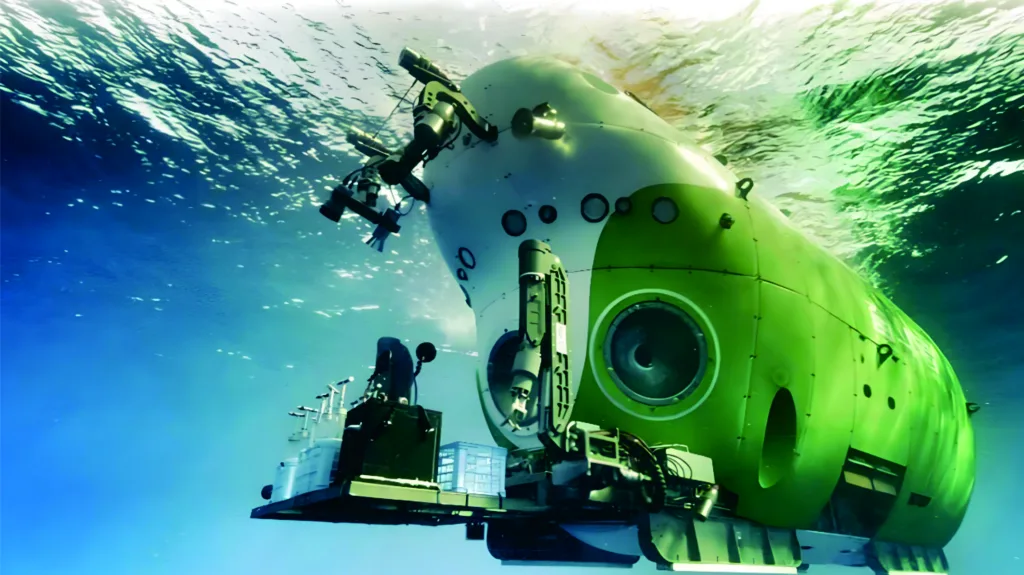
Nuclear Bastion: Immortal Metal in Molten Salt Reactors
In fourth-gen reactors, CLAM stainless steel forms CrF₂/Cr₂O₃ composite films in 650°C molten fluoride salt, limiting annual corrosion depth to 5 μm. This material is already used in China’s TMSR project.
Future Challenges: New Frontiers Beyond Limits
As extreme environments evolve, traditional stainless steel faces new trials:
1. Hydrogen Energy: Hydrogen embrittlement reduces 316L elongation by 40% in high-pressure H₂.
2. Space Exploration: Atomic oxygen erodes ISS stainless steel at 0.1 mm/year.
3. Ultra-Deep Geothermal: Mantle drilling demands super stainless steel for 800°C/400 MPa.
Nanostructural Revolution
– Grain refinement to 50 nm quintuples strength.
– Gradient materials: Surface Cr concentration reaches 35%, core remains at 12%.
– Self-assembled monolayers: Octadecylthiol-modified surfaces achieve >150° contact angle.
Smart Responsive Materials
– Temperature-memory alloys: Phase transition controlled within ±2°C.
– Self-healing microcapsules: Release sodium benzoate corrosion inhibitors upon damage.
– Photocatalytic coatings: TiO₂/Cr₂O₃ composite films decompose organic pollutants.
The Institute of Metal Research’s nanocrystalline stainless steel boosts Cr diffusion rates by three orders of magnitude via grain boundary engineering, achieving zero corrosion in simulated Venusian atmosphere (460°C/92 MPa CO₂).
Philosophical Insights from Eternal Steel
Stainless steel’s evolution reveals not just material science breakthroughs but profound survival wisdom: true strength lies not in absolute rigidity but in rapid-response defense systems; enduring success depends not on flawlessness but on self-repairing resilience. As human civilization ventures into the deep sea, space, and Earth’s mantle, this “strengthened-by-adversity” intelligent steel will continue forging legends in the kingdom of metals.